THE VERSATILITY OF ZINC. A number of metals have been found to be useful in manufacturing small and medium sized parts for most industries but zinc has remained to be the most popular due to its versatility, stability, and cost-effectiveness. The use tin and lead materials have decline since the die casters started using other metal alloys as aluminium, magnesium, and zinc. Zinc has been known to outperform other metals in die casting due to its strength and durability. A number of industries are known to rely on various types of zinc parts as components for their products or as their main product line. From simple shapes to more complex shapes, zinc is a preferred choice of metal to use in die casting.
Zinc is versatile enough for use in any of the two methods of die casting, hot-chamber machine and cold-chamber machine. It is also tool-friendly as it does not damage the hardened tool steel dies. Using zinc as a material for die casting parts allows for more flexibility as zinc can handle not only simple shapes but more complex, multi-cavity shapes as well. Various types of zinc parts made through die casting are able to withstand extreme heat and are wear resistant.
Various types of zinc parts are used in various industries. They can be finished easily depending on the manufacturer’s preferences. Zinc parts such as faucets, studs, connectors, circuit plates, golf clubs and so many others are products of die casting processes. The vastness of the industries where these zinc die casting parts are used is testament to the great value these products are able to deliver both to the manufacturer and to the end-user.
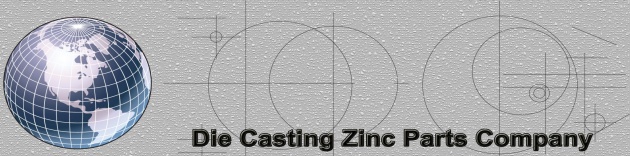
To get a price for zinc die casting parts or zinc die casting tooling, call toll free 800-524-8083 and ask for sales. Or email us at
sales@diecastingzinc.com for a fast response on a price quote.